
Finally, connect the SW pin to digital pin #4. Now connect the CLK and DT pins to digital pins #2 and #3, respectively. Begin by connecting the module’s +V pin to the Arduino’s 5V output and the GND pin to ground. Let’s hook up the rotary encoder to the Arduino. Now that we understand how the rotary encoder works, it’s time to put it to use!
ARDUINO MILLIS LCD BUTTON PRESS HOW TO
Each time the knob is turned in either direction by just one detent (click), the ‘CLK’ output goes through one cycle of going HIGH and then LOW. In this tutorial for beginners Ill teach you how to detect whether a button is being short or long pressed using millis(). This output is used to determine the direction of rotation.ĬLK (Output A) is the primary output pulse used to determine the amount of rotation. When the knob is depressed, the voltage goes LOW.ĭT (Output B) is similar to CLK output, but it lags behind CLK by a 90° phase shift. SW is the output of the push button switch (active low).
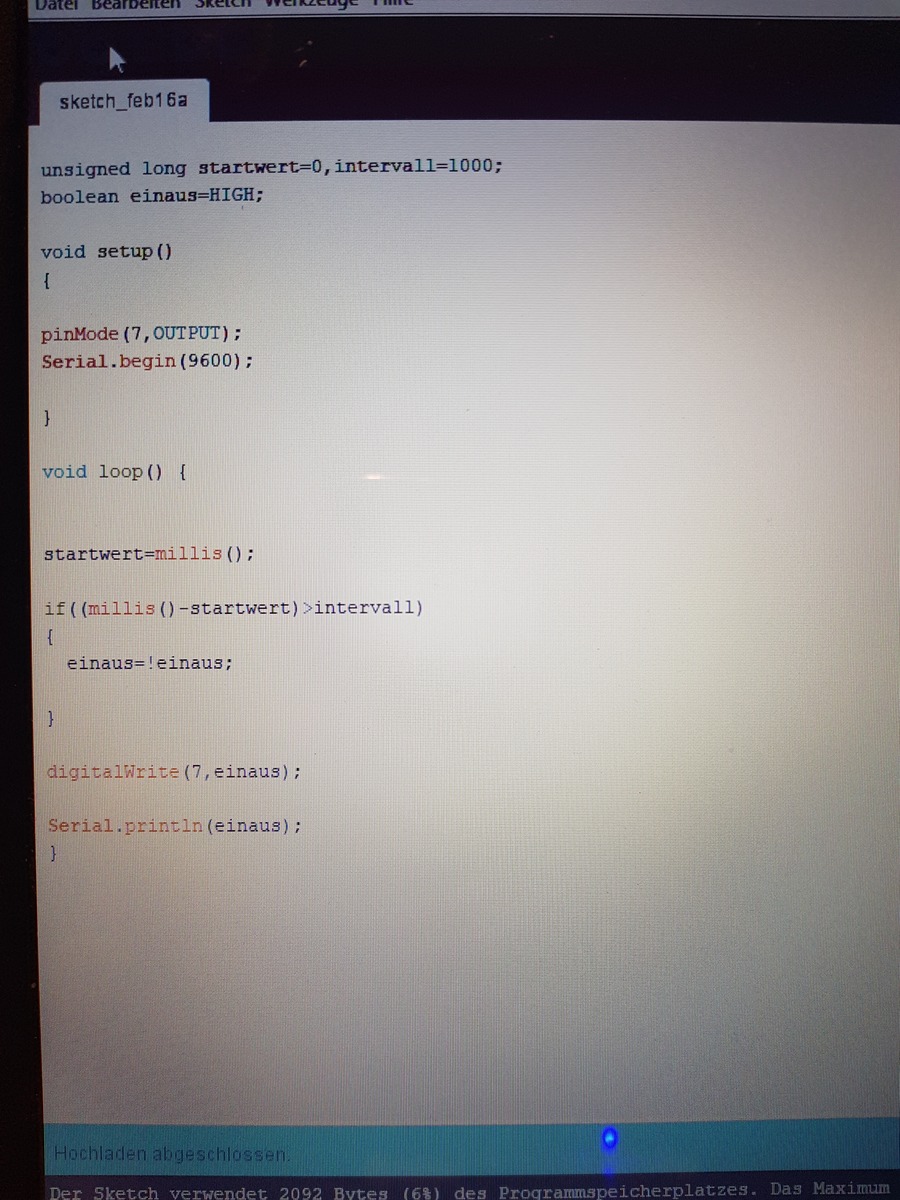
VCC is the positive supply voltage, which is typically between 3.3 and 5 volts. It also has two contact pins A and B, as shown below. Inside the encoder is a slotted disc that is connected to pin C, the common ground. I think the solution above is only good, when you run this function only one time.
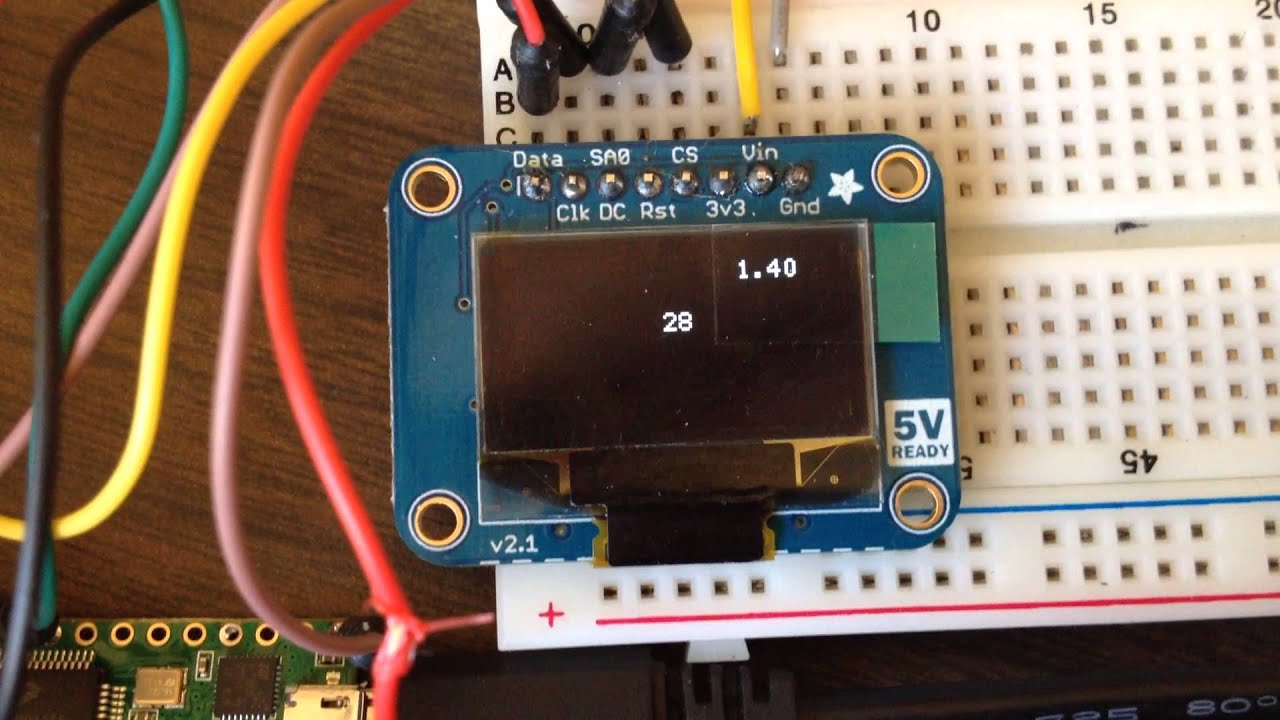
For the search you can use: button debouncing microcontroller or button state change microcontroller. I plan to add additional 'button pins' for. 1,553 1 12 17 asked at 14:50 Patrick Bucher 143 1 1 5 You can ask google how they solve this problem in c with microcontrollers. Several of these need to eventually be running, most likely three, so using delay() won't work. It is intended to power a relay and offer a visual cue to when the cycle is over. Rotary encoders, on the other hand, are used in situations where you need to know the change in position rather than the exact position. I am trying to use the millis() function to turn on a pin for a specified interval then turn off and turn on a second pin. Potentiometers are used in situations where you need to know the exact position of the knob.

Rotary encoders can rotate 360° without stopping, whereas potentiometers can only rotate 3/4 of the circle. Rotary encoders are the modern digital equivalent of potentiometers and are more versatile. The rotary encoder used in this tutorial is of the incremental type. In this tutorial I'll teach you how to detect whether a button is being short or long pressed using millis(). The absolute encoder reports the exact position of the knob in degrees, whereas the incremental encoder reports the number of increments the shaft has moved. Rotary encoders are classified into two types: absolute and incremental. The most common application of a rotary encoder is the volume knob on a car radio.Ī rotary encoder is a type of position sensor that converts the angular position (rotation) of a knob into an output signal that can be used to determine which direction the knob is turned. We are surrounded by rotary encoders without even realizing it, as they are used in so many everyday items, from printers and cameras to CNC machines and robots.
